Application
Note 101
Testing Air Bag
Inflators
at
Atlantic Research Corporation
The Task: Recording Transient Data
Recording multi-channel time-related data
during transient events can be a difficult data acquisition
problem, but transient testing is common in some industries.
Two obvious examples are crash testing and testing of explosives.
These applications require recording once-occurring high-speed
transient data so that the amplitude-time relationship of
several data channels can be accurately compared.
Today, the preferred solution to most testing
requirements uses digital data acquisition systems because
they make data easier and faster to process, analyze, and
store. Yet, when you use digital systems for transient
testing, you must employ special care to design a
recording system that faithfully captures the time-amplitude
characteristics of the data without adding distortion caused
by the digital process. That requires careful attention to
several important system considerations:
·
The system requires very high channel sampling rates to
capture an accurate representation of the waveshape.
·
Crosstalk between channels must be eliminated or minimized
to prevent amplitude distortion.
·
Preservation of inter-channel relationships requires that
all channels be sampled simultaneously and controlled
by a common precision clock.
·
The latency of the host computer must not add time-related
errors to the data.
Traditionally, digital systems employ multiplexed
signals in which multiple channels share one or more high-speed
analog-to-digital converters. The disadvantages of the multiplexed
approach include:
·
Channel-to-channel interference caused by insufficient
amplifier bandwidth and parasitic capacitance.
·
Channel sampling rate dependent upon the number of channels.
·
The need for complex and unique high-speed communications
interfaces.
·
These systems usually require external signal conditioning
and amplifiers for low-level sensor inputs.
To overcome these problems, Neff's System
495 uses a proven, wide range, guarded differential amplifier-per-channel
technique with a dedicated high-speed analog-to-digital converter
for each channel. Features include:
- A true differential amplifier-per-channel
with ranges of ±5mV FS to ±10.24V FS in 12 programmable
Steps
- A tri-filar wound transformer on every
channel to protect against high frequency common mode
noise
- Bridge conditioning with programmable
excitation and auto-balance built in
- Six-pole filter with four programmable
cutoff frequencies
- Dedicated 1 MHz, 12-Bit ADC or 250
KHz, 14-Bit ADC per channel
- Dedicated plug-in memory with up to
64 MSamples/Channel
System
495 Data Acquisition & Recording System
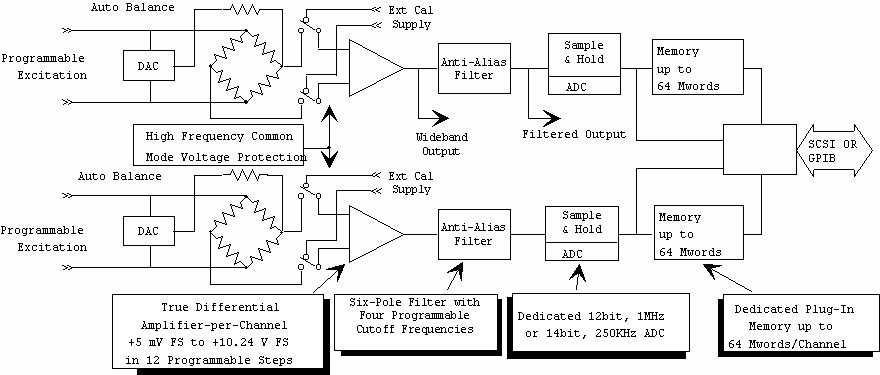
Features
- Differential Amplifier and ADC
Per Channel
- 12 Programmable Full Scale Gain
Steps
- 4 Programmable Filter Steps
- Simultaneous Sample & Hold
- 1 MHz Channel Sample Rate at 12-bits
- 256 kHz Channel Sample Rate at
14-bits
- 1 MHz Aggregate Real-Time Throughtput
- Dual Speed Clock
- Programmable Bridge Excitation
Voltage
- Program-initiated Bridge Auto-Balance
- Bridge Excitation Read Back
- Shunt-R Calibration
- Voltage Substitution Calibration
This design provides the features that are
important to high-speed transient recording systems:
- Very high channel sampling rates
to 1 MHz: With the dedicated ADC per channel transient
recorder design, only the ADC limits sample rates.
- No crosstalk: Each channel
is independent with no multiplexing or shared circuits.
- Negligible skew: All channels
are sampled simultaneously and controlled by a common
precision clock.
- Independent of computer latency:
System clocks control sampling rate, triggers initiate
recording and data is stored on-board. This eliminates
errors caused by the inability of the host computer
to pace the high-speed recording process.
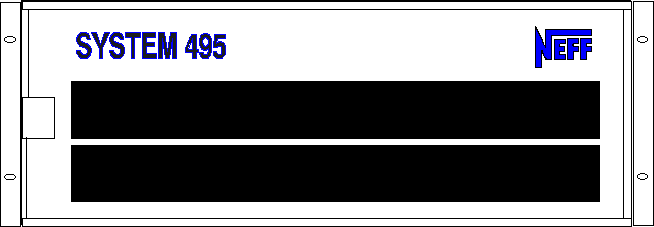
Inflator Testing
at Atlantic Research Corporation
Atlantic Research Corporation, a division
of Sequa Corporation, designs and builds inflators for automobile
airbags. An inflator is basically an explosive device with
somewhat predictable characteristics. ARC has facilities in
Knoxville, Tennessee and Camden, Arkansas. Their corporate
offices are in Gainesville, Virginia.
At each of the inflator facilities, there
are bays designed to test all the different styles of inflators
built by ARC. Multiple pressure measurements along with firing
circuit characteristics are collected beginning at the instant
of firing and continuing for several milliseconds thereafter.
Neff high-speed data acquisition systems are critical to the
operation of these inflator test bays.
The Knoxville, Tennessee manufacturing plant
uses the Neff acquisition system to do Lot Acceptance Testing.
There, the company produces several styles of inflators and
a production run of one style of inflator is classified as
a lot. Samples from each lot are tested to verify performance
against an established standard. Lot acceptance or rejection
is based on the pressure performance of each sample.
ARC Knoxville is expanding and upgrading their
Neff System 490 equipment to the System 495. The new systems
provide them with data transfer rates that are faster by a
factor of 20.
Also located at Knoxville, the engineering
staff is responsible for the design and support of inflators
built by ARC, and for the Engineering Prototype Lab where
new designs are built and tested. This lab also uses the Neff
data acquisition system for all of its pressure data collections.
ARC, Camden Arkansas, is responsible for design
and manufacture of the inflator energetics. Lot inspection
energetics, and new design energetics are installed in take-apart
inflator hardware and deployed in a pressure tank. The Neff
system is, again, used for data acquisition.
ARC chose the System 495 by Neff for the upgrade
of these lab facilities because it allows easy conversion
and expansion, faster transfer rates and preserves the existing
test capability. One other very important issue, the proven
reliability demonstrated by the System 490 encouraged ARC
to look to Neff when they needed the new equipment.
The Test Process
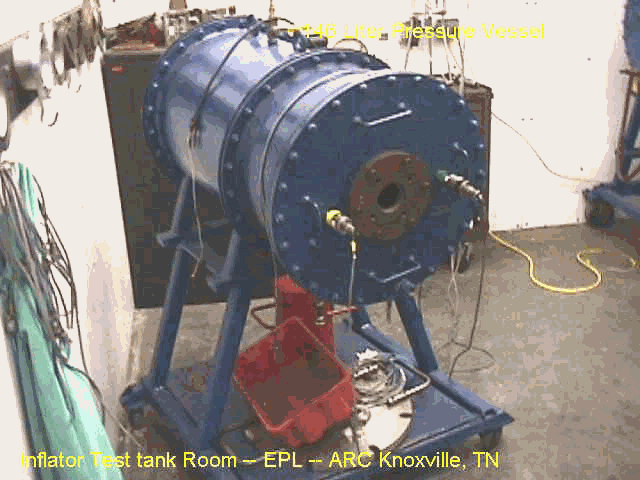
Inflator testing is done in special test bays.
To set up a test, inflators are installed in fixtures that
are attached to, or located inside a pressure vessel. The
physical size of the inflator basically determines the physical
size of the pressure vessel used; The standard sizes of pressure
vessels are 1 cubic foot, 60 liter, 100 liter and 146 liter.
Pressure transducers are installed in the pressure vessel,
and sometimes on the inflator body.
The system includes the trans-ducers, the
System 495 and a personal computer with custom software. Each
pressure transducer and the ignition current signal is assigned
a separate channel. The system is armed and the ignitor is
fired with the high-energy current pulse. As pressure builds
inside the tank the System 495 records pressure at the various
points within the tank along with the characteristic of the
current-pulse.
The System 495 amplifies each data channel
using a wide bandwidth differential amplifier. A 6th order
low-pass Bessel filter with four program selectable cutoff
frequencies filters the amplified data. This anti-alias filter
removes unwanted high frequency noise and sensor ringing.
A sampling A/D converter converts the data into digital information.
Data samples are temporarily stored in DRAM
memory, with a separate plug-in memory module provided for
each channel. ARC uses the 256Ksample module. After the test,
the host computer retrieves each channel's data over a standard
SCSI interface.
ARC uses the System 495 “Block Record” operating
mode. In this mode, blocks of data are recorded, initiated
by an external trigger signal. When the trigger signal is
received a programmable number of samples are recorded.
The System 495 samples and records the high-speed
analog transient data at sampling rates up to 250KHz. Memory
and sample rate management circuitry is provided to control
all channels. This circuitry includes a programmable sample
rate clock, 24-bit memory address register and 24-bit sample
counter. Sampling can be clocked by the internal 5 MHz clock
or by an external TTL (or 5V CMOS) level clock. ARC takes
advantage of the internal sample rate clock to acquire time-multiplexed
data. Others sometimes use the external clock feature to synchronize
sampling with external events. A control register bit selects
the clock to be used. The internal clock is programmable from
0.298 Hz to 2.5 MHz in 200 nSec steps.
Other Important System 495 Features
and Specifications
System Channel Capacity: Multiple-enclosure
495 systems can be interconnected in a master/slave array
with the master providing a common clock to all enclosures.
Each 7-inch high 19-inch rack case can house up to 16 data
channels. Sixteen cases can be interconnected for a system
with 256 data channels.
Bridge Transducer Conditioning: A
plug-on Bridge Conditioner Mode Board is available for bridge-transducer
applications. It provides facilities for mounting bridge completion,
shunt R cal and balance limit resistors. Single, two and four
arm bridge circuits can be used with either local or remote
excitation sensing. The excitation supply is programmable
from 0 to 10 volts with a 12-bit DAC. Maximum operating output
current is 100 mA, and is short-circuit protected. Auto Balance
is programmable.
Operating Modes: The System 495 can
operate in two different modes; the Pre/Post event trigger
mode and the Block Record mode. When operated in the Pre/Post
mode, A/D data is written continuously to memory prior
to the receipt of a trigger signal; new data overwrites old
data in a circular manner. When the trigger is received, sampling
continues until a programmed number of samples are recorded.
The memory then contains N samples taken after receipt of
the trigger signal and (Available Memory - N) samples taken
before the trigger.
The host program polls the System 495 status
register to determine when recording has stopped. Next, the
host reads the current memory address pointer location and
subtracts the sample count value to determine when the trigger
signal occurred. The host then reads the channel's memory
data into a file. The various parameters used for recording
can be appended to the front of the file for use in future
data reduction and display.
The block record mode is used
to record separate blocks of data, each started by receipt
of a trigger signal. The host computer sets the System 495
memory address pointer and specifies a sample count value.
When a trigger signal is received, a programmed number of
samples are recorded starting at the specified memory address
location. The host polls the System 495 to determine when
recording has stopped then reloads the new address pointer
and sample count values.
The next trigger signal initiates the next
record block providing the system has been rearmed. After
the required number of record blocks has been recorded, the
host reads the channel memory data into a file with numbered
record blocks.
Recording Trigger: A trigger signal
is used to start recording acquired data into channel memory.
Three methods of generating the trigger signal are provided:
an external logic level, an analog level threshold detection
on one channel, and program control. Control register bits
are provided to enable external TTL and analog level detection
trigger modes.
The external TTL logic signals
may be either pulses or level transitions of either polarity
selectable by jumper. The analog level detector
initiates a trigger signal when a channel's output signal
level exceeds a preset threshold level. The threshold level
is defined by an 8-bit value (7 bits plus sign) ranging from
-10.24 to +10.24 volts. Resolution is 80 millivolts. Polarity
is programmable so that a trigger can occur when the signal
goes either more positive or more negative than the threshold
level. Recording of the programmed number of samples continues
even if the signal level falls back below the trip point.
Program control is primarily
used for calibration and checkout before a test is performed.
The host computer can position the memory address pointer,
define a sample count value and start recording. With a known
input signal, system accuracy tests can be performed. The
address and sample count registers can also be checked.
Real Time Monitoring: In addition
to storing data locally in memory, a subset of each channel's
data can selectively be transmitted to the host at an aggregate
rate of 1MHz for monitoring or recording. The host computer
can read the current A/D data values of all channels in the
system. This is a "real time" monitor function accomplished
by executing an input scan list. Each channel will return
the current A/D register contents at the time it is read.
The host computer can use this data to drive an external display,
and to test setup and system calibration.
Other Specifications:
Full-Scale Input: 12 programmable steps provide bipolar
input ranges from ±5 mV to ±10.24 V
Full-Scale Accuracy: ±0.1% of FS at zero frequency
Full-Scale Stability: ±0.02% of FS at constant temperature;
±0.005%/°C
Input Impedance: 10 Megohms shunted by 500 pF
Common Mode Voltage: ±10 Vdc peak AC operation, ±30 V
without damage
Common Mode Rejection: 66 dB + gain in dB to 120 dB max,
dc to 60 Hz with 350-ohm imbalance
Filter: 6-pole Bessel filter with four programmable cutoff
frequencies. A plug-in resistor network determines each frequency
over the range of 100 Hz to 200 KHz. Default frequencies are
10 KHz, 20 KHz, 50 KHz and 100 KHz.
Phase Coherency: Phase shift matched channel-to-channel
within 5 degrees with amplifiers on same gain and filter step,
dc to cutoff.
Weight: Each case (without amplifier/ADC cards) weighs
30 pounds.
Acknowledgements:
Charlie Woods at ARC Camden, Arkansas
Rick Robbins at ARC Knoxville, Tennessee
Special thanks to William Stout at ARC Knoxville, Tennessee
for providing details.
|